In foundries, in some cases, the businesses involved had very difficult maintenance and operating circumstances, due to the extreme conditions, which both humans and equipment had to bear. A tough and aggressive environment, extremes of temperature, coupled with extended operating conditions, and a high level of availability, quality and productivity requirement, with the best possible health and safety standards, being necessary at all times.
Regardless of the location, it is critical that the highest level of maintenance is practiced, if a successful process is to be envisaged. It is difficult to categorize the various foundry conditions under one heading, as they will apparently vary depending on their operating process, products, and production capabilities. Maintenance processes simply involve the operations of inspecting, lubricating, replacing or updating equipment, so as to enable the item or service to sustain an operational performance, at optimal levels. Regular maintenance also improves the service life, at an economical value, linked with the life cycle costing and properly contributing to the levels of profitability.Types of Equipment
Some of the common maintenance equipment used in foundries are -
|
Foundry Maintenance Foundry maintenance, as like other industries, should ideally start with the purchasing move. Once it has been agreed to invest in new systems and equipment, be it direct from the manufacturer or from any other source, consideration should be given to the total life cycle of asset. Apart from the normal day to day operational costs, the evaluations should include the effect of the depreciation on the accounts and the routine maintenance costs, how often will it be necessary to have the item out of functioning for overhaul or maintenance, and of course, what will be the cost of disposal, in due time, and could it have a resultant effect. In few cases, it may be worthy to have another equipment, if down time is to be avoided.
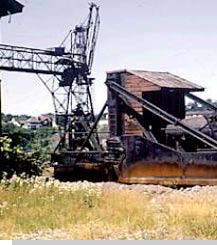
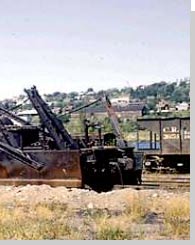
In the case of a foundry it is not only crucial to center on the important items of equipment, located at the brunt or sharp end of the company operations, but also to give consideration to every item, which goes to make the plant work. This strategy will range from the reception of materials to handling, right through to the equipment on the shop floor. However, there are numerous, just as significant contributions given by the materials handling, sorting, preparation, weighing equipment as those given by the different, equally important, ancillaries.
For example, the air compressors should, wherever possible, be ideally located so as to be capable of facilitating air of a quality cognizant of the requirements.
If there are many controls necessitating a high quality air condition, then consideration can be given to providing a separate main for this specific function, with all the necessary specifying attachments equipped, such as dryers, pressure regulators etc.
The source of the air is also a crucial factor, as it can be counter productive to have the air intakes in a dusty atmosphere, necessitating a higher level of filtration to satisfy the cleanliness requirements. The setting of pressure levels is also important, along with the sizing of compressed air mains, as air velocity within a main can be elusive in its own right.