Castability, a critical aspect of casting process, is the ease of producing a casting with minimum costs, defect and lead-time.
Castability analysis is a very important process, which guides in achieving the optimal product design of the desired quality. Castability analysis involves three stages, namely, which are discussed in detail below,
- Casting Simulation
- Casting Cost Estimation
- Castability Checks
Casting Simulation This involves analysis of processes such as mold filling, grain structure, stress analysis, distortion and solidification. It also takes in account models of product and tool equipment like cores, parting, mold layout, feeders, gates etc., along with temperature regulated properties of mold and part materials and finally the process parameters such as pouring rate, temperature etc. The results from these studies are applied in predicting casting defects like hard spots, blowholes, cold shuts, shrinkage porosity, cracks and distortion.
This method requires expert handling of the inputs, which are normally not easily accessible to the product designers. However, best results can be achieved by concurrent engineering approach wherein the foundry and tooling engineers actively participate in the product design phase and simultaneously evolve the product, tooling and process design thereby ensuring mutual compatibility.
Cost Estimation Cost estimation is very vital in the entire casting process. The cost factor is directly proportional numerous aspects of the product such as weight, part metal, shape complexity, number of holes, type of parting line, feeders involved, yield, metal to sand ratio, quality requirements, production quantity, tooling material, elements in the mold like feed aids, filters etc and finally the desired lead time. Taking in account these factors the cost coefficients can be determined by regression analysis of past data. Past data refers to data extracted from sufficient cases of complete and correct process details. These coefficients are updated regularly and employed in assessing the process design and also applied in the “what-if” design analysis to lower the costs.
The drawback of this approach is that it can be utilized adequately only in case of castings which are similar to previous cases on which they can be correlated with respect to part metal, casting process and geometry.
Castability Checks Castability checks are very relevant and there are many guidelines documented to handle the common casting related issues. The figures illustrated below reflect some on the common problem scenarios and their recommended solutions.
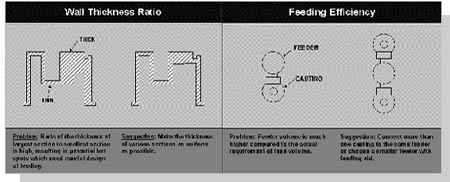