Die design is an emerging field in which cost-effective methods are employed for the production of a diverse range of things. But for maximizing the profits it is absolutely necessary for the die designers to work in collaboration with die casters at the initial stages. This helps in solving problems related to tooling and production. It also helps in maintaining balance so that costs can be reduced to the minimum. For instance if dies with slides are required, it would increase the cost of tooling but decrease metal use.
CONSTRUCTION: A die is basically made in two sections: the fixed die half and the ejector dies half. The fixed die half is the cover half and the latter makes the removal of castings possible. Certain modern dies also have slides, cores or other such sections so that holes, threads etc. can be produced in the casting. Molten metal are injected into the mold under high pressure. Two methods are used for this purpose: Hot chamber method or Cold chamber method. When the die machine is closed the two die halves are locked.
TYPES:Single cavity dies that produce one component only.
Multiple cavity dies to produce many identical parts.
Unit dies that produce diverse parts at a time.
Combination dies to produce different parts for an assembly.
FIRST STEP IN DIE DESIGN: One of the first steps involved in designing a die is the selection of a suitable alloy. The characteristic properties of a particular alloy must be studied in detail keeping in mind the purpose for whish the die is required. Mostly alloy tool steels are used for the purpose. Zinc proves economical for small casts. Aluminum is light weight and has strength at high temperatures. Magnesium is the lightest alloy and the easiest one to machine. Copper is strong and has tremendous wear resistance. Lead and Tin have high density and are used for making parts having very close dimensions.
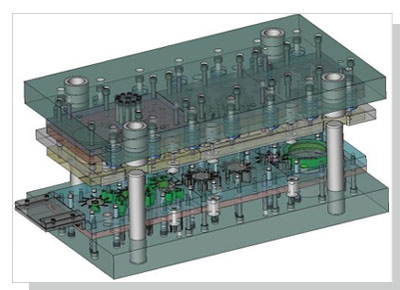
COST OF MATERIALS:The next thing is the cost of materials that are required. We should not be more concerned about the cost per cubic pound or cost per cubic inch but should take a holistic view. For example as metals are stronger, they are required in less quantity than plastics for a particular purpose.
INNOVATIONS:Innovations are being done in die design, the casting process and in the alloys used. As a result more and more markets are coming under its ambit and strong, varied and high precision products are being manufactured.