This process can be categorized as similar to that of permanent mold method. Here as the molten metal is being poured, a permanent metal mold revolves about its axis at high speeds ranging from 300 to 3000 rpm. This can be in horizontal, vertical or inclined positions. As a result, the molten metal is centrifugally thrown towards the inside mold wall. There it solidifies after cooling. It's usually a fine grain casting with a very fine-grained outer diameter.
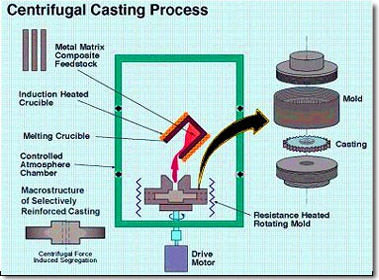
Molds for centrifugal castings can be divided into three types.
The Permanent Mold: Made of steel, iron or graphite. Inside surface is coated with a thin refractory wash to increase mold life. The mold is preheated before coating, so as to dry the coating and improve the adherence to the mold surface.
Rammed Mold: It consists of a steel metal flask, lined with a layer of refractory molding mix. The inside lining is coated with a refractory wash which is baked until dry and hard.
Spun or Centrifugally Cast Mold: In the metal flask a predetermined mass of refractory material in slurry form is poured.
The flask on rotation makes the refractory materials centrifuged onto the wall of the flask. The rotation is stopped and the liquid portion of the slurry drained off. It leaves the mold with a refractory coating, to be baked until dry before use.
Features of Centrifugal Casting- Castings can be made in almost any length, thickness and diameter.
- Different wall thicknesses can be produced from the same size mold.
- Eliminates the need for cores.
- Resistant to atmospheric corrosion, a typical situation with pipes.
- Mechanical properties of centrifugal castings are excellent.
- Only cylindrical shapes can be produced with this process.
- Size limits are upto 3 m (10 feet) diameter and 15 m (50 feet) length.
- Wall thickness range from 2.5 mm to 125 mm (0.1 - 5.0 in).
- Tolerance limit: on the OD can be 2.5 mm (0.1 in) on the ID can be 3.8 mm (0.15 in).
- Surface finish ranges from 2.5 mm to 12.5 mm (0.1 - 0.5 in) rms.
Applications of Centrifugal Casting:
Typical materials that can be cast with this process are iron, steel, stainless steels and alloys of aluminum, copper and nickel. Two materials can be cast by introducing a second material during the process. Typical parts made by this process are pipes, boilers, pressure vessels, flywheels, cylinder liners and other parts that are axi-symmetric.
There are two types of Centrifugal Casting: