There's a a huge market evolving for Powder Metallurgy. The strides that it has made especially over the past quarter century is no doubt a remarkable achievement. No doubt world wide metal powder production is exceeding 1 million tons, with largest consumer of the products being the automobile sector. The process is about heating metal powders just below their melting point temperatures when metal parts are formed. The process starts with the making of metal powder.
Source: EPMA
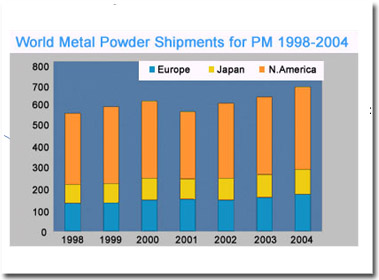
Methods of Metal Powder Production:
Solid-state Reduction | Atomization | Electrolysis | Chemical |
Solid-state
Reduction The selected ore is crushed and then mixed with a reducing agent like carbon and passed through the furnace. Where a reaction results in a product of cake of sponge metal. It is then crushed, separated from non-metallic parts, sieved and then made into a powdery form. A remarkable feature of this process is that as no refining takes place, the purity of the end product depends upon the purity of the metal. Refractrory metals are generally made by the hydrogen reduction of oxides. |
|
In this process, molten metal, is made into small droplets then frozen before they come into contact with each other or with a solid surface. This is done by subjecting the droplets to high energy jets of either gas or liquid. Gases used can be nitrogen or argon while the liquid used can be water.
This process is applicable to all metals with average melting points, low melting points like tin or tungsten and other high melting point materials.
These days a process called Centrifugal Atomization is being increasingly used, where droplets of molten metal are released from a rotating source. This process can take two types of forms: -
- Where a cup of molten metal is rotated in a vertical axis that throws of the droplets.
- Rotating Electrode Process (REP) – Here the metal bar is rotated at high speed either horizontally or vertically. While the free end of the metal bar gets melted by plasma or electron beam.
The advantages of using Atomization Process
- Since it gets carried out in sealed vessel, in controlled atmosphere and even in vacuum, a clean powder is produced
- There is considerable reduction of nonmetallic inclusions in the powder form as there is no contact with the refractory.
- Particularly useful for production of Alloys in the powder form.
Electrolysis
Metals can be deposited either in spongy or powdery state by making available conditions such as electrolyte composition and concentration, temperature and current density.
This is then subjected to washing, drying, reducing, annealing, and crushing before high-purity and high-density powders is yielded. Copper is the chief product, but iron, chromium, and magnesium powders are also produced and in select cases materials with high melting points like tungsten can also be produced.
ChemicalChemical treatments involve thermal decomposition, oxide reduction and precipitation from solutions. The unique feature of this process is that the powders treated this way can vary in properties, yet have closely controlled size and shape.
Thermal decomposition is very often used to process carbonyls. These powders, once milled and annealed, this way can exceed 99.5 percent purity. Oxide-reduced powders are often termed as spongy due to pores present within each particle. While solution-precipitated powders has the features to narrow down particle size distributions and obtain high purity.
Powder Metallurgy Techniques
Powder forging
![]() Like conventional powder Metallurgy, the heated compact called preform is withdrawn from the furnace and coated with a high-temperature lubricant. This is transferred to a forging press where it is close-die forged (hot worked). Forging allows plastic flow. Which reshapes and densifies the preform metal to its final configuration and eliminates porosity. |
The Powder Metallurgy techniques can be pre dominantly divided into two processes.
Conventional Methods - Press and sinter processingThis process comprises the following steps:
- Metal powders blended and fed into a die.
- Compacted into the desired shape.
- Ejected from the die,
- Sintered (solid-state diffused)- This takes place at a temperature below the melting point of the base material in a temperature controlled furnace.
- The Sintering process creates metallurgical bonds between the powder particles, adding the requisite mechanical and physical properties to it.
Advantages of Press and sinter processing
- Low manufacturing costs Close Tolerances in the finished products.
- Elimination of the need of Secondary machining operations.
- Availability of wide variety of materials
Application of Press and sinter processing
Typically Press-and-Sinter Product are used in automobile, agriculture, hydraulics industries to produce cams, pressure plates gears, sprockets, ratchets, levers, clutch plates, bearings, bushings etc
Limitations of Press and sinter processing- Presence of residual porosity lowers some of the physical and mechanical properties
- Tooling and the press tonnage capacity dictates the size and shape on parts to be fabricated.
Non-conventional Methods Metal Injection Molding
Gives producing capability for complex shapes in bulke quantities. The process uses very fine metal powders (often less than 20 micrometers) which are blended with a binder (various thermoplastics, waxes) into a feed stock. There it is granulated and then put into multiple cavities of a conventional injection molding machine. The “green” component is removed, the binder is also extracted by way of thermal or solvent processing. Finally The component is sintered (solid-state diffused) in a controlled atmosphere furnace.
Advantages of Metal Injection Molding:- Capacity to produce mechanical properties nearly equivalent to wrought materials.
- Good dimensional tolerance control.
- Molded parts offer a nearly unlimited shape and geometric-features.
- High production rates by using multi-cavity tooling.
Production of medical, computer peripherals, electronic packaging, consumer products etc possible.
LimitationsPart size, limited with most components generally not exceeding 250 g.
Isostatic Pressing (Hot and cold ) Powder ForgingUsed for producing large parts with near-net shapes and different complexity. The metal powder is kept within a flexible membrane (hermetic container) this acts as pressure barrier between the metal powder and the pressurizing medium like water or gas that surrounds it. The use of this procedure facilitates homogeneity of the final product along with uniform compaction pressure.
Advantages Isostatic Pressing:- Can produce parts much larger in size than other PM processes,unlimited range of complex shapes and geometric features.
- Useful for difficult to compact and costly materials such as superalloys, tool steels, stainless steel, titanium.
- Highly efficient material utilization
- Using HIP, parts can be produced that offers fully dense material with isotropic mechanical properties equal or even better to those of cast and wrought materials.
Application of Isostatic Pressing:
Wide use in aviation defence, medical equipment to produce cutting tools, automotive cylinder liners, corrosion resistant components etc
Limitations of Isostatic Pressing:- Isostatic pressing is useful in general only to small production runs, typically less than 10,000 pieces annually
- Costlier than other Powder Metallurgy processes.
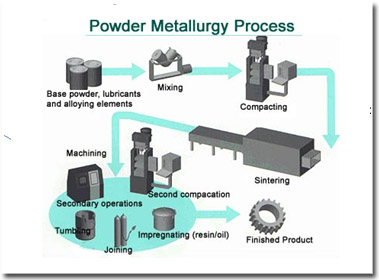
The container is typically made up of a rubber or elastomeric material. Water or oil is the pressurizing medium. Due to absence of Die frictional forces, the powder compact has a higher and more uniform density. However, in CIP processing, the part must be sintered (solid-state diffused) after it is removed from the mold.
Hot Isostatic Pressing (HIP)Metal or glass is used for making the hermetic container for the metal powder. The pressurizing medium is gas (inert argon or helium). At high temperatures, the hermetic container deforms plastically and the powder is compacted within it. No further sintering process is needed here as the combination of heat and pressure during the process eliminates its need. Also the removal of the HIP container after processing is an additional requirement here.