The method of boundary element has the aforementioned method as another variation. The basis of this method is to find that path of feed which passes through any of the point within the casting. The hot spot which is local is then arrived at following this path. It is assumed that the path of feed would lie alongside the thermal gradient which is highest. The heat conduction law by Fourier could be used in order to determine the gradient. The law is as follows :
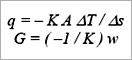
Here the thermal gradient is given by G+ , whereas the flux of heat at a prescribed point within the casting in a direction that is given is represented by w=q/a. The gradient and the flux of heat have a zero value in the direction that is tangential to the isotherm which passes through that point. They are maximum in the direction that is perpendicular to the point. At a given point within the casting the greatest thermal gradient's direction and magnitude has proportionality with the resultant vector of vectors of thermal flux in each direction that originate from that very point.

- The division of the volume of casting into numerous pyramidal sectors that originate from the considered point is done. Each of these pyramidal sectors has a solid angle that is small. For the computation of the vector of flux, the content of heat (which is proportional to the volume) and the surface area of cooling are determined for each sector.
- Until and unless the resultant vector of flux becomes zero(or comes approximately close toe zero for the purpose of computation), a step is taken along the direction of the resultant vector of flux, a location which is new is arrived at, and the repetition of the same computation is done.
- The location of the hot spot is the last location so arrived at. The path of feed is taken to be the curve alongside which the repetitions are done.
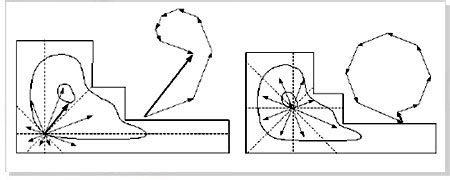
Within the casting, the identification of various hot spots can be done if the computation is started from numerous seed points. Each of such seed points lying at the casting's different regions.
Fig: The resultant flux vector points to the hot spot
The verification of the method can be done easily for a shape that is 2D. The representation of the length of the vector of flux is done by a/2. Here 'a' denotes the distance between the point at which the ray intersects and the boundary of the casting. The direction of the bisector of the angle of the sector can be taken as the ray's and the vector of flux's direction for that sector.
- In comparison with the FEM or the FDM methods, this method is strong as it takes care of small errors during computation of vector of flux at any point (due to the non-availability of precise thermal and physical data) by automatically correcting them in subsequent repetitions.
- Also the greater efficiency of VEM methods over FDM and FEM methods ( the requirement of memory is low, and are faster by about 10-100 times) in the identification of hot spots in castings that are quite complex shaped, is established.
Fig: Top: Simple casting along with the feeder; middle: Solidification with directions (path of feed); bottom: forward moving solidification in the section that is at the centre.
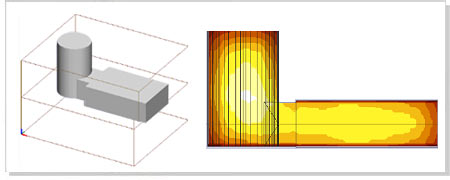