A foundry may pour a casting having little knowledge of how a casting cools down or how the metal freezes within the mold. However, if proper planning is not done the result can be gas or shrink porosity within the casting. To improve the quality of a casting the foundry engineer studies the geometry of the part and plans how the heat removal is to be controlled.
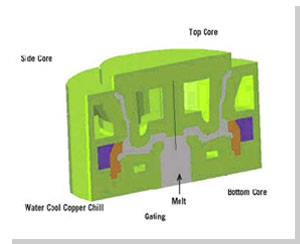
It is important to find the suitable casting geometry so as to meet the structural and solidification shrinkage needs. For some alloys, finding the right geometry can be very simple. For other alloys, obtaining that geometry is the real essence of superior casting design. In the case, that geometry is not found for difficult alloys, the foundry engineer should resort to "thermal trickery" to achieve fluid flow and heat transfer patterns, which the geometry fails to deliver.
Thermal trickery is a highly effective technique but is expensive. By eliminating thermal trickery with good design, it is possibleto achieve cost less production, processing and assembly.
The conventional method of obtaining the casting geometry is by sending blueprint drawings to the foundry. However, the development of computer hardware and software for making and analyzing solid models has enabled a quantum leap in the use of section modules to add features like increase in the stiffness of structural components and reducing the stress within them. In fact, these tools are making the power of metal casting geometry much more accessible to design engineers because they enhance significantly the ability to visualize in three dimensions. Casting Geometry plays a significant role in the casting yield.
Advantages of Good Casting Geometry- Reduces defects, post casting operations, and rejected castings
- Significantly reduce energy and environmental impacts
- Saves energy
- Improves overall quality and life of casting