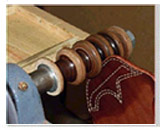
Burnishing can be defined as a process in which a smooth but hard tool using sufficient pressure burnishing is rubbed on the surface of the metal. This helps to flatten the high spots by allowing plastic flow of the metal.The edges of the metal can be smoothened by pushing it through a die that will smooth out the burrs and the blanked edge caused by the die break
Roller Burnishing : Roller Burnishingimproves the finish and size of surfaces. Both internal and external surfaces can be burnished using an appropriate tool. It involves the cold working of the workpiece. The roller burnishing pressure to be applied depends upon factors like ductility, tensile strength, diameter, shape of the rolls etc.
Burnishing Tools: Burnishing tool is the only option wherever there is need for accurate size and smooth surface finish. Burnishing tools are generally made of high Speed Steel or Carbide material, that are positioned in slots along with a retaining cage.It has a number of tapered and polished precision rollers. An inversely tapered mandrel is used for rotating the rollers.
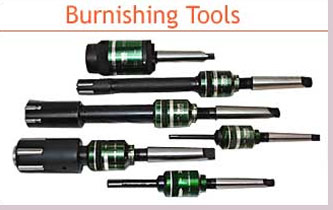
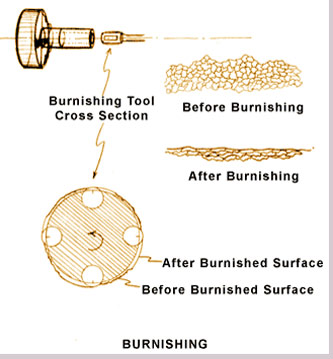
Burnishing tools can be fitted with Lathe, Drilling machine or CNC machine and can be operated easily without the operator having any specific skills.
Advantages of Burnishing Process:- Improves the size and finish of revolution like cylinders and conical surfaces.
- Internal and external surfaces can be burnished .
- Improves surface hardness.
- Increases, wear-resistance, decreases fatigue and fights corrosion.
- It also eliminates the Grinding and Honing processes which can be costly.