There is no substitute for good, fine casting sand for metal casting. The experiments with the use of common foundry sand proved to be completely disappointing for packing and retaining its shape when dry. Casting of sand is the simplest and most versatile of all casting methods used to produce castings.
There are various types of sand used in casting. These different types of casting sand have their own advantages and disadvantages. The type of metal required to be cast influences, which additives and what gradation of sand is used.
Some of the most common types of casting sand used in hobby foundries are -
- Green Sand
- Natural
- Synthetic
- Oil Tempered Sand
- Core Sand
- Sodium Silicate
- Baked Binder
Green Sand
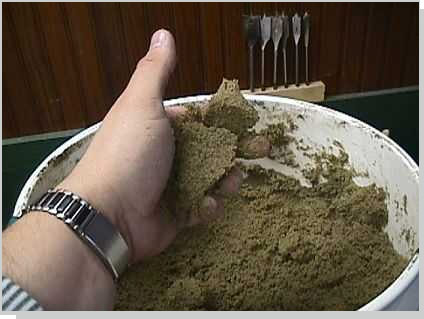
Natural sand is the one that is obtained from ground. Characteristics of natural sand may vary depending on source it was obtained from. The clay content will be about 11 – 30 %, and the clay is generally kaolin.
Synthetic sand is more commonly practiced these days. Synthetic sand means clean, graded sand in the required grain size in which clay can be added as desired. This type of sand permits the users to more closely control the attributes of the sand. There are three basic types of clay, which you can add to your sand -
- Kaolin, or Fireclay
- Western Bentonite
- Southern Bentonite
These different clays have their own advantages and drawbacks. The bentonites are generally preferred over other types of clay because of their high bonding power. This gives two advantages -
It means less clay is required to give the desired strength and hence the sand will be more permeable. In other words there will be more open spaces between the sand grains to allow the gases to escape from the mold. As these is less clay, less water is required to get the sand to the point where it has the desired strength. It means that there will be less gas generated and as the sand is more permeable it will escape easier.
Western bentonite gives greater dry / hot strength than the other two types. Southern bentonite is known for its superior green strength and greater permeability than the same quantity of Western, though only moderate dry / hot strength. Due to this reason, southern bentonite, or a mixture of the two, is preferred for aluminum casting.
Oil Tempered Sand
Oil tempered sand has a special binder instead of the clays that are mentioned above. The binder reacts with the oil instead of the water like previous clays. As there is no water involved there is no steam produced when the metal is poured. Due to this there is a lesser need for venting of the mold and hence the sand does not need to be as permeable. As the sand can be less permeable, a finer mesh of sand can be used that will result in a finer finish on the cast part. Moreover, as there is no water to evaporate, the sand will stay functional longer, even if it is not in a sealed container.
Oil tempered sand, however, has some disadvantages. The sand needs to be mulled when you are first making it. After the initial mulling you can get by with a aerator / fluffer till the time you need to add some more binder or oil wherein it should be mulled again. There are few people who have designed their own mullers they have found to be good enough. There is a possibility for the oil vapor to ignite, if the mold is shaken too early. This is not very likely to happen, however you should be aware of it.
So if you are working with low temperature metals and have some way to mull the sand than there is a lot to prefer oil tempered sands. Different brand names for the binder of oil tempered sand are available in the market.
Core Sand Among the various kinds of binders available for core sand, the most commonly used by hobby foundry professionals are – sodium silicate and baked core. Here baked sand is referred to low technology sand that is available to average hobbyist. The advantage of this type of baked core is its low cost and easy availability.
Sodium silicate is a liquid, which you mix with core sand, and for this you need plain clean sand. When the sand is packed in the core box, the core requires to be hardened. The core can be hardened by just leaving it exposed in air wherein the CO2 will harden it. That time for the hardening of core depends on the size and complexity. There are some ways to get CO2, you can find a tank and a regulator from a welding supply shop. This could be highly expensive if you are making a few cores. You can design some sort of adapter in order to make use of the small CO2 cartridges used for paint/pellet guns. Otherwise, for the most economical mode, you could make use of chemistry. The addition of vinegar and baking soda produces CO2, you simply requires to control where the gas goes. The benefit of CO2 process is that you don't require access to an oven, and the additional equipment required is comparatively cheap and simple. The cores produced from this method will be as accurate as your core box as you gas the core while still in the box and do not remove until it is hardened.